High performing food & beverage manufacturers maintain a CI program to offset annual inflation and protect GM% without raising prices. Do you?
With inflation moderating, it is easy to forget the stress inflation put on the P&Ls of food & beverage manufacturers in 2021-2022. Large CPGs understand the importance of offsetting cost inflation each year through annual cost savings programs. In the middle market, however, such programs are much less common but equally if not more important.
Example 1: $100mn Branded Food & Beverage Manufacturer with 34% Gross Margin
While 3% cost inflation may not sound like a lot, as shown below, a $100mn branded manufacturer with a 34% gross margin and 16% EBIT margin would experience a 12% decline in operating profit and a 0.4x increase in financial leverage if it were to experience 3% annual net inflation in its cost of goods sold.
Of course, the manufacturer could raise its prices 3% and protect its margins – but if its competitors don’t do the same, it risks losing market share and experiencing negative operating leverage (see exhibit 1).
Example 2: $100mn Non-Branded Food & Beverage Manufacturer with 20% Gross Margin
Annual productivity programs are even more important for lower margin manufacturers, as the lower the operating margin the greater the impact of net cost inflation on the P&L. As shown below, a $100mn non-branded manufacturer with a 20% gross margin would experience a 24% decline in operating profit (compared with 12% decline in the previous example) and 0.8x increase in leverage if it did not offset the impact of 3% annual inflation (see exhibit 2).
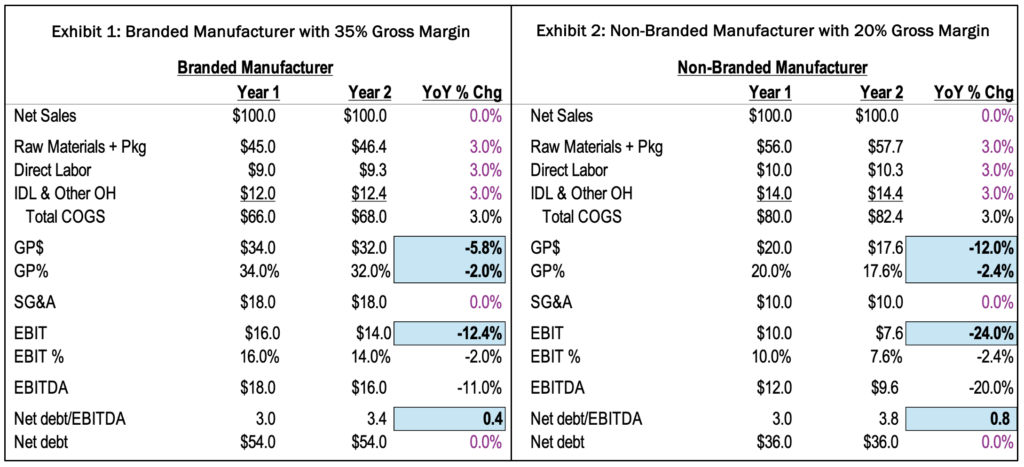
The magnified impact of inflation for lower margin manufacturers reflects the difference in the ratio between COGS and operating profit. For the higher margin manufacturer, 3% net cost inflation translates into a profit decline of 12.4% because its COGS are ~4x its operating profit…whereas in the case of the lower margin manufacturer, the ratio of cost of goods to operating profit is ~8x.
As demonstrated above, maintaining a robust Continuous Improvement (“CI”) strategy and implementing annual CI plans focused on offsetting COGS inflation is critical to protecting margins and price competitiveness, while providing the valuable fuel to drive investments in top line growth. Each manufacturing site has its own unique challenges that will necessitate specific solutions, but the tools and methods are tried and true across facilities and industries.
Key elements of an effective CI Execution Plan
Saphineia has decades of experience developing strategies which have cumulatively delivered hundreds of millions of dollars in cost savings, while simultaneously building a culture of ownership and accountability on the shop-floor. Below is a high-level sample outline for a CI plan that Saphineia can help you build.
- Set the strategy that aligns with the company’s vision – clear goals and process
- Prepare the execution plan
- Establish savings and sustainment targets by manufacturing site
- Establish savings targets itemized by category of type of savings
- Focus on projects with direct EBITDA savings (not hypothetical) and beware of unintended consequences (projects that save $ in one place but cost $ in another)
- Identify specific projects and cross functional owners
- Create the tracking and project sustainment structure with change management tools
- Governance structure in place to track performance against targets
- Short term interval controls ensure project sustainment
- Focus on the most typical loss areas
- Improve productivity: increase output per labor hour, reduce overtime, etc.
- Reduce raw and packing material losses: scrap, overfill, inventory write-offs, etc.
- Reduce OH costs: IDL costs, 3 rd party storage, transportation, etc.
- Reduce the cost of poor quality: Rework, quality write-offs, quality returns, etc.
- Reduce other sources of EBITDA loss: Late charges, violation fees, etc.