Grade inflation in education
Last December, the Wall Street Journal article, “Grade Inflation Makes A the New C”, addressed secular grade inflation in U.S. higher education. The article referenced an anonymous survey by The Harvard Crimson in which 69% of Harvard’s 2022 graduates told the Crimson that their GPA was 3.8 or higher, up from 54% in 2020. Just 9% of graduates said their GPA was 3.5 or below!1
Grade inflation in finance
Many would say a form of grade inflation exists in finance too. Who can forget the 2008/09 Global Financial Crisis, which many blame, to a degree on S&P and Moody’s due to what were, in hindsight, unreasonably favorable ratings and outlooks for financial institutions and high-risk mortgage-backed securities?2
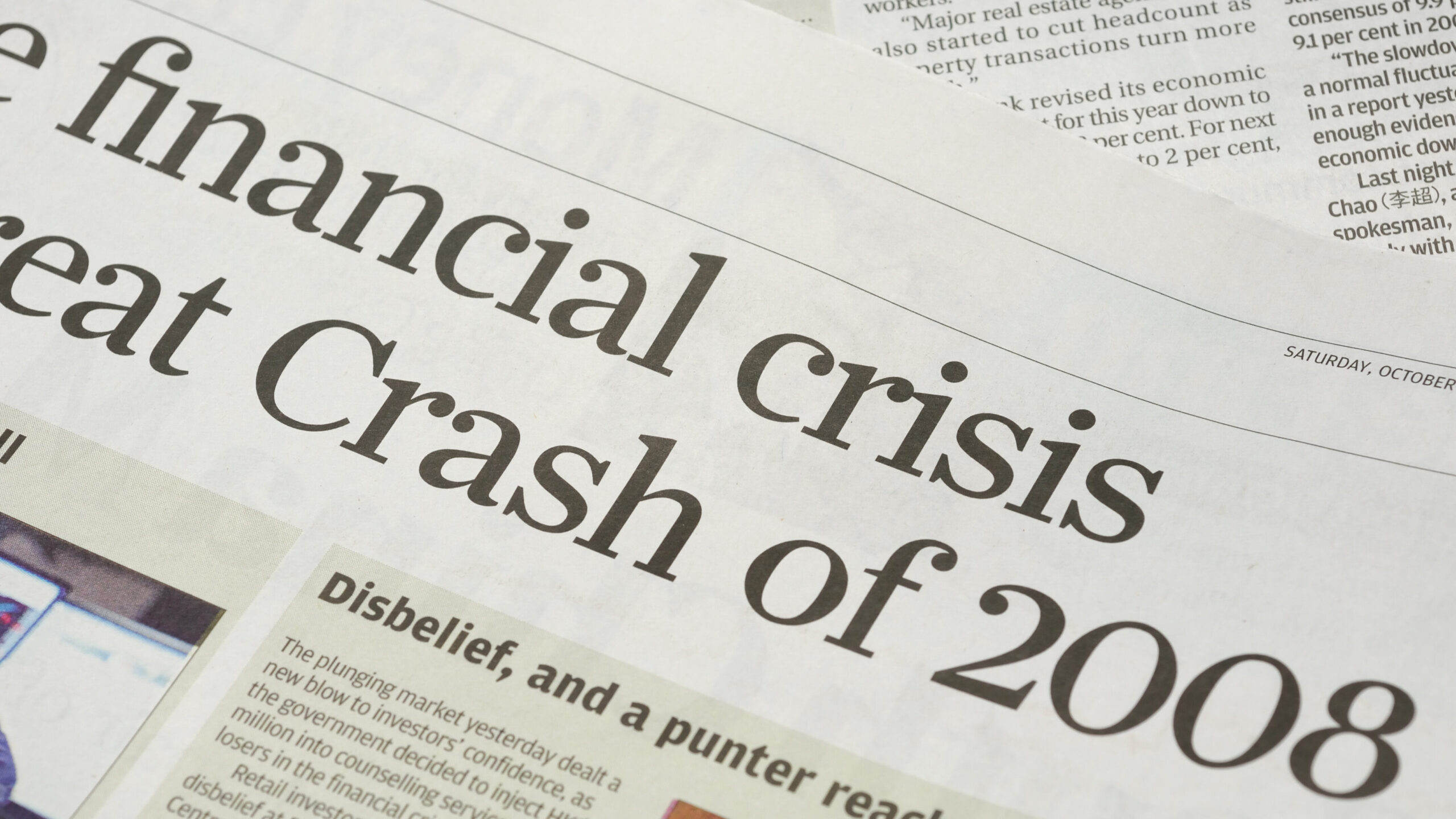
Grade inflation exists in Food & Beverage manufacturing too
Similar to how the finance industry relies on the rating agencies for credit ratings, the Food & Beverage industry relies on external grading systems in the area of Quality & Food Safety (Q&FS), with most manufacturers implementing one of two globally recognized standards (SQF or BRC). These standards serve two purposes: providing widely accepted Q&FS criteria that manufacturers should continuously strive to meet; and to demonstrate to actual and potential customers that their facilities meet the high standards of these programs.
According to the SQF Institute, which administers the SQF Program:
By becoming SQF certified, your company will not only enhance its reputation as a trusted and reliable partner in the food industry but also open doors to new business opportunities. SQF certification serves as a powerful differentiator, setting you apart from competitors and instilling confidence in your customers and stakeholders.
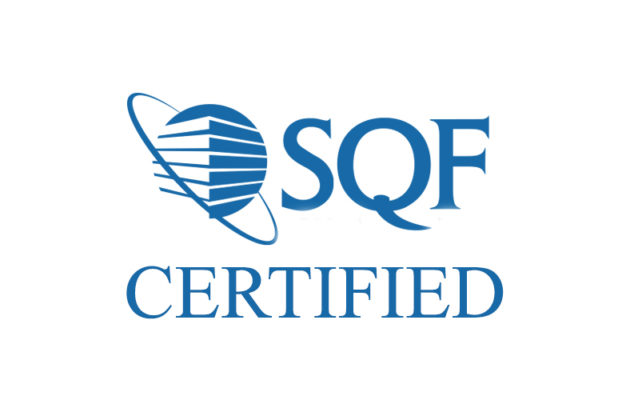
Here’s the rub: out of the approximately 12,000 SQF audits conducted globally in 2021, the average score was a 94.3 out of 100!3
This observation is not meant to malign the SQF Program or SQF auditors, both of which are valuable pillars in protecting our nation’s food supply. In our experience, most auditors effectively utilize the “carrot” of a high score as a mechanism to continually push manufacturers to improve their Quality & Food Safety systems year after year – a laudable and valuable objective. After all – the goal of the system is a food supply chain we can trust.
Still, if nearly everyone gets an A on their SQF score, how are manufacturing executives, customers and investors supposed to assess the Quality & Food Safety risks associated with a given manufacturing facility and/or differences between facilities?
Advice for investors and customers: Do your own work
Our advice: just as sophisticated fixed income investors don’t rely on credit ratings but rather perform their own analysis of a borrower’s creditworthiness, we recommend that investors and customers of food manufacturers (e.g. retailers, brands that utilize co-mans and foodservice providers) do their own work and reach their own conclusions. Take the time to evaluate a manufacturer’s quality systems and practices yourself to determine whether they are indeed ‘walking the talk’ when it comes to Q&FS.
Lessons for manufacturers: Don’t just cram for the exam
In our experience, some manufacturers view quality as a final exam they need to pass and cram for weeks before their annual audit to make sure their plant ‘shows well’. This approach is facilitated by the fact that manufacturers know the exact date of their SQF audit two out of every three years (with the 3rd year being unannounced, but within a specific time range).
Manufacturers who take this approach to quality should keep the following in mind: each year in the United States, there are approximately 300-400 recalls of Food & Beverage products, and companies experiencing a recall incur high costs, including large expenses associated with physically recalling the product from the market and higher recall insurance premiums.
Beyond these “hard costs”, recalls can come with substantial ‘soft costs’ too, such as reputational damage and lost business. In some cases, food safety issues can even force a manufacturer to close a facility – as Pepsico did earlier this year at its Danville, Illinois Quaker Oats plant due to repeated salmonella outbreaks.4 In a few cases, manufacturers have been held corporately liable for their actions5 and, in the most extreme situations, corporate personnel have gone to prison.6
Just like in school, cramming may get you a desired test result, but it doesn’t generally lead to long term retention of the subject matter. To consistently deliver high quality products requires robust systems and practices that are managed and monitored as a regular course of business. This means to not view the SQF results as a check the box activity or to rely on the SQF score as the definitive representation of the maturity of your quality systems. Rather, just like human beings routinely undergo an annual physical, we recommend that at least annually, manufacturers do their own deep dive into their Q&FS practices over and beyond their work in preparing for their SQF or similar audit.
Here’s the good news: investing in quality is good for business
In one of the definitive books on quality, Quality is Free by Phillip B. Crosby7, the author estimates cost of (poor) quality8 ranges from at 2.5% of revenues at best-in-class manufacturers to as high as 20% of revenues for companies whose management lacks comprehension of quality as a management tool.
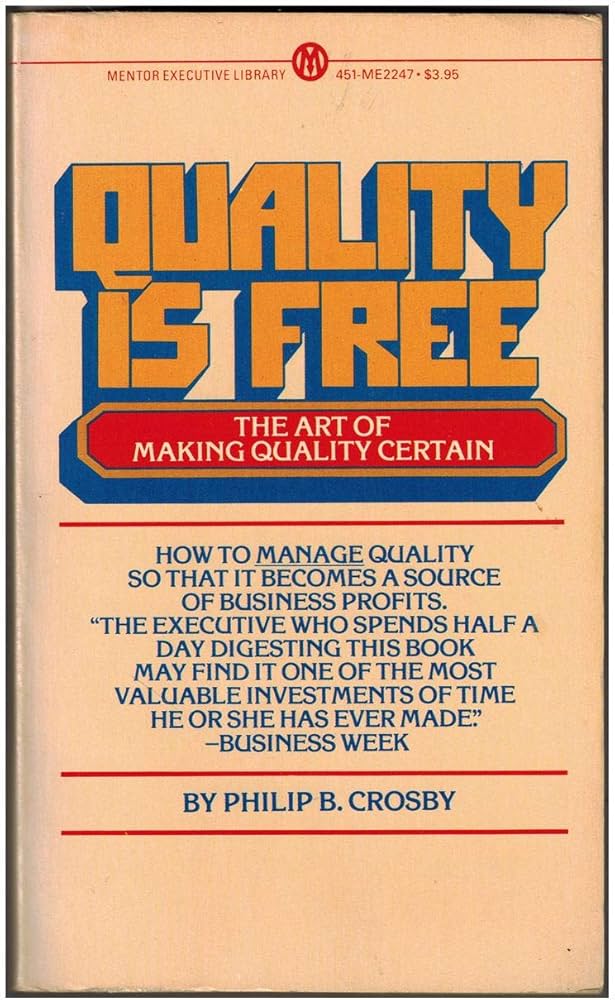
As Crosby’s research highlights, Food & Beverage manufacturers pay for quality, one way or the other: that is, they can pay ‘a little’ by investing consistently in maintaining strong Quality & Food Safety systems or they can pay ‘a lot’, in the form of lost business, product recalls and/or high costs associated with poor quality. Moreover, and just as importantly, most customers recognize and value quality, which allows manufacturers with strong quality systems to be more successful in attracting new business and keeping it.
In sum, while scoring well on a quality audit is important and necessary, in our opinion it is not sufficient. We submit that manufacturers, customers and investors will be well served by doing more than simply relying on the latest audit score.
- The Graduating Class of 2022: By the Numbers. The Harvard Crimson (2022). GPAs rounded to 1 decimal place. ↩︎
- The Credit Rating Controversy, Council of Foreign Relations (February 2015). Critics of rating agencies often blame the “issuer pays” model, whereby the company raising money pays the rating agencies to issue the ratings, which the public can access free of charge. ↩︎
- SQF 2022 Professional Update Webinar ↩︎
- FDA Blasts PepsiCo for Response to Salmonella Positives Over Four Years at Quaker Oats’ Danville, Illinois Plant (https://www.foodprocessing.com/) ↩︎
- Office of Public Affairs | Blue Bell Creameries Agrees to Plead Guilty and Pay $19.35 Million for Ice Cream Listeria Contamination – Former Company President Charged | United States Department of Justice ↩︎
- Office of Public Affairs | Former Peanut Company President Receives Largest Criminal Sentence in Food Safety Case; Two Others also Sentenced for Their Roles in Salmonella-Tainted Peanut Product Outbreak | United States Department of Justice ↩︎
- Crosby, Phillip, B. (1980), Quality is Free, the Art of Making Quality Certain, by Philip B. Crosby (The Penguin Group) ↩︎
- Costs of poor quality include rework, scrap, overfill, holds, returns, labor, damages, etc. ↩︎